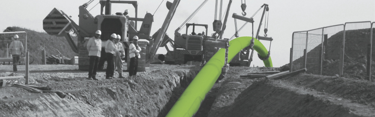
Bringing projects together
We have a team of engineers that draw on a number of backgrounds that including civil engineering, mechanical, electrical, manufacturing, geotechnical and environmental engineering disciplines.
From design management and project start-up, through to quality, engineering and site management, inspections and audits, we have a rich portfolio of experience across a number of disciplines. This enables us to offer a broad range of services that can complement your team and ensure you get the most from your project.
Discover our latest projects
Filter
Filter
Sort
1 - 6 of 6 results
Here to achieve, validate and demonstrate compliance
Our expert consultants are available to ensure compliant and effective processes for asset design, build, maintenance, and operation.
Contact our experts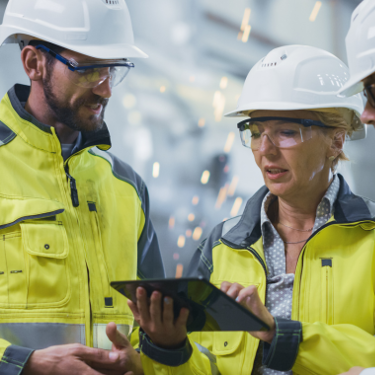