Delivering Materials & Equipment Certificates Training courses to ensure continued competence and wellbeing in the gas industry
Published: 25 February 2025
The gas industry is high-risk and high-profile. Ultimately, the integrity of the network relies on every link in the supply chain operating to international quality standards with every person committed to identifying and choosing quality – especially when no one is looking. Otherwise, things can go wrong, often with catastrophic results. Supplies can be lost, the environment can be damaged, networks and contractors sued, reputational damage and – in the worst case – loss of life can occur.
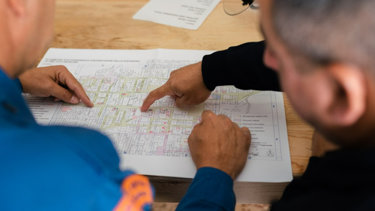
In the UK, we are lucky to have a closely regulated gas industry with an enviable safety record. But it wasn’t always this way. The early days of the National Transmission System were marred by test failures, caused by unknown material sources and poor manufacturing techniques. From the late 1960s to the early 1990s, however, the industry worked hard to oversee supplier quality assurance and develop standard material specifications. From that point, things got much better, and have been improving ever since, thanks, in no small part, to proper materials and equipment certification.
Understanding the challenge
While the gas industry is undeniably safe by international standards, several factors have made it even more important to assure materials and equipment certification.
- The national transmission network is no longer an integrated network. There are a number of distribution networks and a national transmission network, each with their own identities and specifications. With such fragmentation comes greater need for knowledge.
- The supply chain is now global, so understanding the integrity of ‘suppliers’ and ‘sources of supply’ is even more crucial, both in terms of security of supply and ensuring component fitness for purpose.
- Reliable training in how to interpret materials and equipment certificates didn’t really exist. People have often found themselves in responsible quality and safety roles, ‘doing their best’ to ascertain the integrity of materials procured, but without formal training.
We were contracted by IGEM – the Institution of Gas Engineers and Managers – to deliver comprehensive training in this field to address these needs and raise industry awareness. The learning would be invaluable for everyone, from design engineers to project engineers and managers, engineering policy managers, site supervisors, inspectors, and quality managers.
Our approach and implementation
Our primary objective was to establish this training as a face-to-face course in which attendees could get hands-on experience with some basic products and scrutinise original material test certificates, all in a learning environment supported with real-life examples.
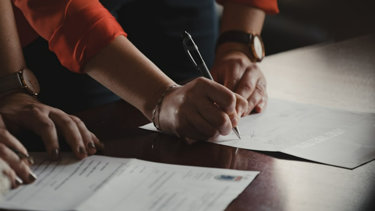
A further aim was to create training that provided an entry-level knowledge base for personnel working in the energy industry, upon which these professionals could pursue specialisms as their career developed.
Our objectives were to provide attendees with:
- The confidence to interpret materials and equipment certificates throughout the energy sector
- The skills to understand and apply the information contained within these certificates
- The ability to verify certificates and documentation, ready to ensure assets are designed, constructed, tested, and maintained safely
- An understanding of the differences between accreditation and certification
- A commitment to the role of quality assurance in safe and effective procurement
- An overview of the varied certification and records required across an asset lifecycle
We have drawn on our rich network of leaders in the engineering industry to create and deliver this training, particularly favouring those people whose backgrounds in high-hazard industry drive their passion for project quality assurance like this. The course comprises presentations, practical activities, and group discussion, and is constantly evolving to keep pace with, and anticipate, regulatory and specification changes in the energy industry.
Impact and outcomes delivered
So far, we have run 24 Materials & Equipment Certificates Training courses across the UK for IGEM. Delegates have included personnel from several gas networks, including Cadent Gas, SGN, Gas Networks Ireland, and Northern Gas Networks, as well as independent delegates from a number of roles across the energy sector.
The training has driven robust learning in the following areas:
- Who issues certificates, e.g., accreditation bodies, notification bodies, certification bodies, and suppliers
- The range of certificates encountered in different environments and processes
- Guidance on the different types of equipment certificates, including ATEX and DSEAR
- The distinction between material Certificates of Conformity and declarations of conformity
- Why traceability is crucially important
Our trainers are committed to ensuring corporate memory is shared with the next generation of technicians, engineers, and managers to ensure the continued competence and wellbeing of the energy industry.
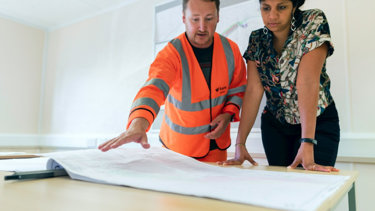
But perhaps most importantly, the feedback from our courses is invariably positive. Delegates tell us how relieved they are to feel properly equipped to interpret certificates. Many more describe how motivated they now are to interrogate certification with real authority.
This course helps create a workforce that understands there is no safety without quality, and that the energy industry is no place for assumptions – however small.
More of our projects...
- Projects
Assessing and improving security of critical assets and site infrastructure
- Projects
Keeping families warm and feeling safe in multi-occupancy buildings
- Projects
Helping David Hardie Engineering secure certification and recertification for ISO 9001, 14001, and 45001 standards
- Projects
Delivering Materials & Equipment Certificates Training courses to ensure continued competence and wellbeing in the gas industry
Here to achieve, validate and demonstrate compliance
Our expert consultants are available to ensure compliant and effective processes for asset design, build, maintenance, and operation.
Contact our experts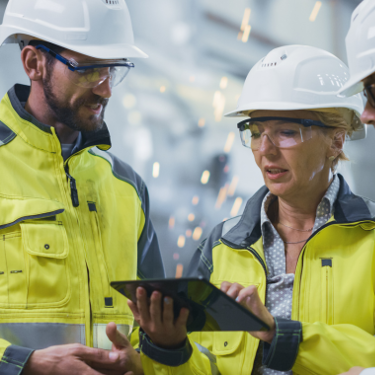