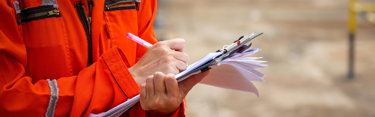
Operation and maintenance
We help gas networks, utilities sectors, contractors, and specialist site managers to achieve and sustain high standards of operations and maintenance. We do this by providing both expert guidance from experienced personnel, and tailored support software which, together, resolve the operational headaches many sectors experience on site.
To enable us to deliver in every context, we have also created our own software – not only to simplify the management of assets, competencies and safe systems of work, but to achieve improved standards of compliance throughout the whole operations and maintenance lifecycle. This means:
- Reduced administration time.
- Paperwork is removed from the worker competencies and permitry processes.
- Comprehensive asset management solutions ensure high quality procurement, use and maintenance of project assets.
- Clients raise their standards of practice, achieve compliance and gain competitive edge at tender.
- Cost savings throughout the project lifespan, safeguarding client companies’ prosperity.
Operation and maintenance services
Mitigate risk, assess compliance, optimise asset life and support cost effectiveness. Our specialist asset survey engineers will report and advise on the health of your asset portfolio.
Services we currently provide for GDNs include: GSMR cut-off surveys, MOB surveys, and CDS surveys on gas distribution pipe works.
Skilled maintenance can prolong the life of expensive assets, safeguards people, and ensures that assets remain compliant with relevant standards.
We maintain low and medium pressure network distribution systems, where services include: installation and maintenance of winter pressure loggers, catheter installations, GSMR cut-offs and remedial works, as well as Mains Pipeline Risk Surveys (MPRS) that examine depth of cover, third party interference risk, environmental and site-specific hazards.
Effective competency management supports safer working practice, reduced risk, and makes sure the right people are mobilised on every project.
We deliver both on-site and training centre competency assurance assessments, and undertake post-completion gas escape audits to support GDN risk management. We also carry out independent audits, investigations and onsite coaching for gas distribution.
Streamlining safety processes using simple mobile devices. Reduced administration time empowers managers to create a safer workplace.
Maximising efficiency, quality, and uniformity of process, SOPs reduce human error and drives compliance with industry regulations.
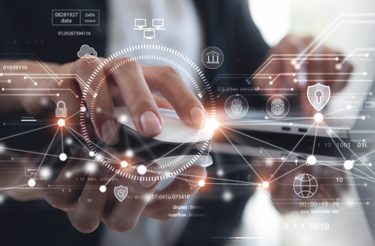
Safe system of work
Cloud based software for safe system of work and standards compliance.
Why QEM?
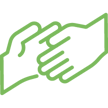
People first
We understand the pressures caused by operating in complex and challenging contexts, and will work alongside your team as supportive equals to reassure and improve.
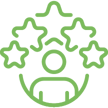
Experience
We’ve worked in engineering operations like yours from before our company was formed in 2003, and can ensure that your operation receives that collective knowledge, experience and drive.
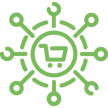
Cutting edge software
We created our own software to resolve the problems we’ve experienced most, and have made it both scalable and affordable for all operations.
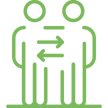
Cross-sector expertise
Our people have considerable experience in managing complex projects in difficult environments across a broad range of sectors.
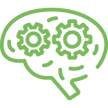
Empowered personnel and improved morale
Our people impart their skills to their client teams, instilling both confidence and ability.
You might also be interested in...
Here to achieve, validate and demonstrate compliance
Our expert consultants are available to ensure compliant and effective processes for asset design, build, maintenance, and operation.
Contact our experts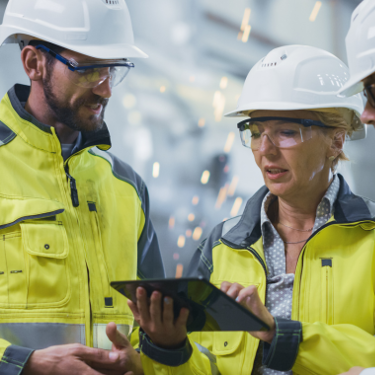